Thought Leadership
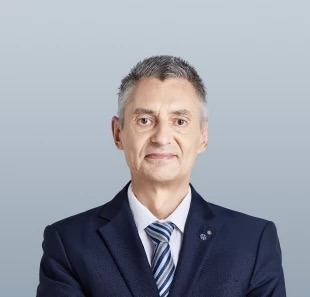
By DC member Karlheinz Zuerl*
Autonomous factories are on the rise in Asia and will spread to Europe in the coming years, albeit with some delay. Europe likes to boast about its progress in Industry 4.0, but Asia has long since moved beyond that and is on its way to Industry 5.0. This refers to unmanned production halls in which only robots are active. These ‘ghost factories’ are made possible by a combination of computer technology, networking, artificial intelligence, robotics and innovative manufacturing processes.
Europe talks up Industry 4.0
The latest ‘World Robotics Report 2024’ from the International Federation of Robotics (IFR) provides figures for 2023. According to the report, almost 4.3 million industrial robots are working in factories worldwide, a historic high. In 2023, more than 540,000 new robots were installed, over half of them (51 percent) in China. Europe accounted for only 17 percent of all new installations. In Germany, the largest European market for industrial robots according to the IFR, growth of only 7 percent was recorded compared to the previous year.
There is a tendency in Europe, and especially in Germany, to gloss over Industry 4.0 with meaningless figures. Studies by industry associations Bitkom and VDMA claim that around 65 percent of companies in Germany use Industry 4.0 technologies. That sounds good, but it is completely irrelevant because every device with a Wi-Fi connection is included in the figure.
BMW is 4.0, Tesla 5.0, China over 4.5
It is significant that the BMW plant in Dingolfing is considered the pride of the German automotive industry because, since 2024, cars that have completed production there have been driving without drivers for quality control purposes. However, this only works with special external sensors along the route and does not mean that the vehicles themselves have autonomous driving capabilities. This is not comparable to the Tesla factory in Fremont, California, where cars travel from the production line to the logistics site completely independently – i.e. without external support. BMW is at level 4.0, Tesla at 5.0. Many Chinese manufacturers are at 4.5 or better in this scenario.
The gap will continue to widen to Germany's disadvantage. The VDMA has forecast a weak year for robot installations in 2025. According to the association, there is hope for a slight recovery in 2026.
Run on digital production twins in Asia
Meanwhile, in Asia, we are seeing a veritable rush for ‘autonomous production twins,’ or APTs for short, in the manufacturing industry to autonomously monitor, control and optimise production processes. An APT combines real-time data, artificial intelligence and advanced networking to create a virtual representation of the production system that can make decisions and adapt processes independently. An autonomous production twin can actively control manufacturing processes and respond to unforeseen events, for example by rescheduling in the event of material bottlenecks; this is becoming everyday practice in more and more factories in Asia's manufacturing industry.
The unmanned factories can reduce operating costs by up to 25 percent, increase productivity by up to 30 percent and reduce error rates by up to 40 percent. This explains the greater competitiveness of Asian Industry 5.0 production. A well-intentioned piece of advice for Western industrial companies: Set up an autonomous factory in Asia, learn how it works, and then adopt this concept for European plants. This approach is not only suitable for car manufacturers, but also for many machine and plant manufacturers. Although sensor technology, software and infrastructure account for around a third of the total costs of setting up an autonomous factory, the higher investment pays for itself in the first year of operation alone thanks to significantly lower wage costs. Added to this is greater flexibility to respond to market changes and higher quality, which reduces rework costs and increases customer satisfaction.
* Karlheinz Zuerl is CEO of German Technology & Engineering Corporation (GTEC). The company helps Western industrial companies overcome challenges in Asia. The focus is on business development, setting up and expanding branches and production facilities, as well as restructuring and turnaround measures to bring mainly automotive suppliers and mechanical engineering companies back into profit in critical phases. Under the leadership of CEO Karlheinz Zuerl, a team of consultants, experts and interim managers is active and can be deployed on site at the customer's premises if required. The CEO himself is available for assignments as interim general manager and for executive consulting. GTEC's list of references includes corporations such as BMW, Bosch, General Motors and Siemens, large medium-sized companies such as Hella, Schaeffler, Valeo and ZF, as well as smaller medium-sized companies that are less well known but are all the more successful in Asia thanks to GTEC.